Features/Application

Fast exposing single cure emulsion. No need other diazo sensitizer.
High viscosity and high solid makes Rotary profile emulsion surface.
Excellent print performance.
Excellent mesh adhesion and encapsulation properties.
Excellent water resistance and easy to reclaim.
Superb resolution and sharp image definition for the fine image reproduction.
Specifications
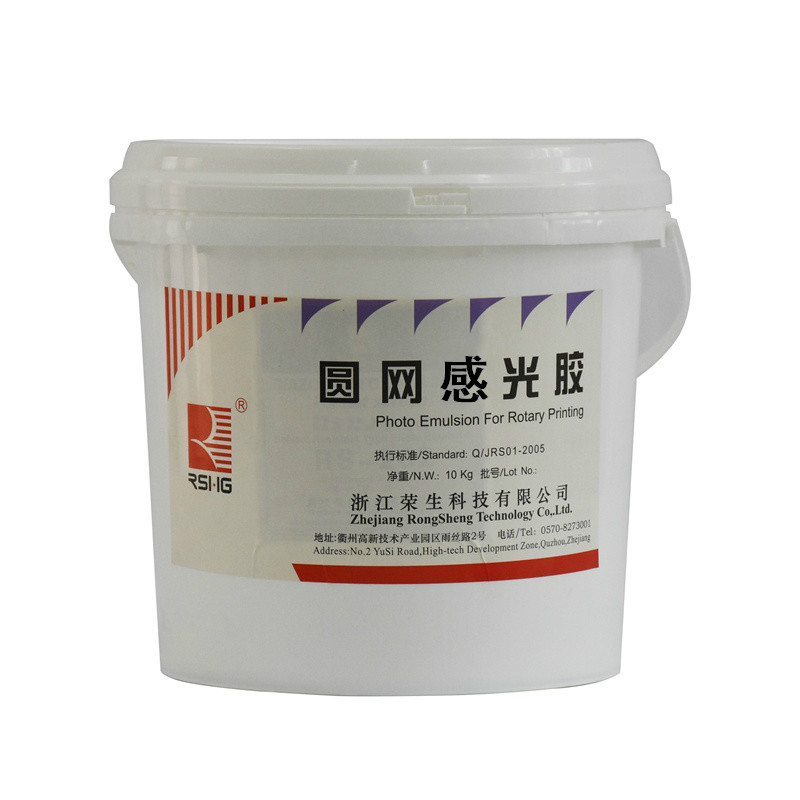
Viscosity: Approx. 7,000 ± 2,000 mPa・s.
Solid Contents: Approx.45 ± 2 %
Packaging Standards: 5kgs set,10kgs set,50kgs drum.
Color: blue or red.
Storage: 1 year at 68°F/20°C.
Pre-coated screens: 8 weeks in complete darkness at 68°F/20°C.
Freezing: protect against freezing.
Solvent Resistance Rating
Solvents | Rating | Solvents | Rating |
Water | Excellent | Methylcellosolve | Good |
Toluene | Fair | Isophoron | Fair |
Acetone | Good | Ethyleneglycoldimethylether | Fair |
Ethylacetate | Good | PGMEA | Good |
Butylcellosolve | Excellent | Ispropyl alcohol | Excellent |
N-methyl-pyrrolidone | Poor | Metylethylketone | Fair |
Butylacetate | Excellent | Butylcarbitolacetate | Excellent |
Cyclohexanone | Excellent | Terpineol | Excellent |
Orange oil | Poor | methanol | Fair |
※24 hours swelling/absorption test results.
Exposure Data
To achieve a good stencil, the mesh must be degreased with a degreaser and must be free of dirt, dust, ink residues and ghost images. Rinse the screen thoroughly using low water pressure to remove any degreaser remaining on the screen. A foaming degreaser helps to determine proper and complete rinsing. See MSDS Information for details. |
Instructions
RT-108 has excellent coating properties on mesh counts of 40-470 threads per inch (16-185 threads per cm). Always start with 1 or 2 coats on the substrate side of the screen to fill the mesh openings; then finish with wet-on-wet coats on the squeegee side to build up the emulsion coating to the desired thickness. The correct coating technique for your process must be determined through coating tests.
Remarks
Dry the screen in complete darkness, or under safe-light conditions,with the screen in horizontal position with the substrate side down.
Temperature, relative humidity and airflow affect the drying time. The screen must be dried thoroughly before exposing to achieve highest resistance to ink and ink cleaners. A temperature of 86°-104°F (30°-40°C) at a relative humidity of 30% -50% and moderate airflow are optimum conditions. Drying at room temperature and in uncontrolled conditions may lead to inconsistent results and varying screen resistance.
Expose with ultra-violet light at a wavelength of 320 - 380 nm. A metal halide lamp provides the best results. Due to the many
variables that determine the actual exposure time, accurate exposure times cannot be given. The following examples are offered as a
guide only:
Lamp: CST CTS DLE engraving machine (DMD technology)
NBC 120T white mesh, coating thickness: 3-5 um.
Expose speed: approximately 19-22CM/Second
The correct exposure time for your equipment and mesh selection must be determined through exposure tests using a step exposure or an exposure calculator films.
Temperature, relative humidity and airflow affect the drying time. The screen must be dried thoroughly before exposing to achieve highest resistance to ink and ink cleaners. A temperature of 86°-104°F (30°-40°C) at a relative humidity of 30% -50% and moderate airflow are optimum conditions. Drying at room temperature and in uncontrolled conditions may lead to inconsistent results and varying screen resistance.
Expose with ultra-violet light at a wavelength of 320 - 380 nm. A metal halide lamp provides the best results. Due to the many
variables that determine the actual exposure time, accurate exposure times cannot be given. The following examples are offered as a
guide only:
Lamp: CST CTS DLE engraving machine (DMD technology)
NBC 120T white mesh, coating thickness: 3-5 um.
Expose speed: approximately 19-22CM/Second
The correct exposure time for your equipment and mesh selection must be determined through exposure tests using a step exposure or an exposure calculator films.